燒結(jié)磚隧道焙燒窯“煤改氣”的工藝分析
摘要:當前,燒結(jié)磚企業(yè)隧道窯采用內(nèi)燃摻配料+外投煤(內(nèi)燃燒磚)工藝方式進行燒結(jié)生產(chǎn),存在大氣污染物治理專業(yè)性難度大,持續(xù)穩(wěn)定達標排放困難等現(xiàn)象。隨著建筑工業(yè)化的推進和裝配式建筑的應(yīng)用,促使燒結(jié)磚生產(chǎn)企業(yè),進行清潔燃料天然氣替代內(nèi)燃燒磚工藝用煤的燃料結(jié)構(gòu)改革,要在原隧道焙燒窯上進行“煤改氣”,涉及窯的結(jié)構(gòu)、燃燒形式、熱工控制及碼坯方式等方面的適應(yīng)性困擾。
關(guān)鍵詞:強氧化燃燒方式、熱工控制、單位產(chǎn)品能耗變化
國內(nèi)燒結(jié)磚的隧道窯焙燒工藝,基本采用摻配具有發(fā)熱值的工業(yè)廢棄物、原煤作為摻配料,在焙燒過程中,少量外投煤作補充,此類內(nèi)燃料+外投煤的隧道窯焙燒方式,俗稱隧道窯“內(nèi)燃燒磚”工藝。
隨著《磚瓦工業(yè)大氣污染物排放標準》、《中華人民共和國環(huán)境保護稅法》、《燒結(jié)磚單位產(chǎn)品能源消耗限額》等法規(guī)、標準的正式實施,加之燒結(jié)磚企業(yè)由于實施治理時間較短,存在著煙氣治理決策不科學(xué)、隧道窯運行工況不穩(wěn)定、煙氣治理工藝不完善、治理效果不理想、治理運行費用比較高等問題,造成企業(yè)不能持續(xù)穩(wěn)定地實現(xiàn)達標排放,對此,面臨較大的大氣污染物治理壓力和無法正常生產(chǎn)的局面,對燒結(jié)磚企業(yè)而言,大氣污染物治理工作,是一項全新的專業(yè)性和技術(shù)性很強的環(huán)保科技工作,燒結(jié)磚企業(yè)缺少經(jīng)驗、缺少技術(shù)、缺少環(huán)保技術(shù)人員等現(xiàn)實條件,迫使企業(yè)針對采用現(xiàn)有“內(nèi)燃燒磚”中,產(chǎn)生較高大氣污染物的原燃料類型,尋求清潔燃料為替代,其中,部分企業(yè)選擇了液化天然氣(LNG)氣化氣或管道天然氣作為燒磚燃料,從而大幅度降低污染物治理帶來的困擾。這是現(xiàn)有燒結(jié)磚企業(yè)在隧道焙燒窯中改用天然氣,簡稱“煤改氣”的主要原因之一。
其次,隨著建筑工業(yè)化的推進和裝配式建筑的應(yīng)用,燒結(jié)磚生產(chǎn)的轉(zhuǎn)型升級也勢在必行,而、提高產(chǎn)品檔次,滿足建筑工業(yè)化和裝配式建筑功能要求,在焙燒過程中,采用清潔燃料天然氣進行燃料結(jié)構(gòu)改革,也是必要的。
1、現(xiàn)有隧道窯內(nèi)燃+外投煤焙燒方式的特征
長期以來,隧道窯均采用的是“內(nèi)燃燒磚”工藝,這種工藝已成為國內(nèi)非常成熟可靠的一種工藝模式,該工藝提供的產(chǎn)品,具有強度高、性能穩(wěn)定、吸水率適中、密實度較高、房屋隔音性能好和防火等優(yōu)點,確保建筑具有較高的質(zhì)量和較長的壽命,作出了較大的貢獻。焙燒窯“內(nèi)燃燒磚”工藝的主要特征是:
A、燃料性質(zhì)
內(nèi)燃燒磚工藝,需要事先將一定的原煤燃料或具有發(fā)熱值的工業(yè)廢棄物摻配到磚坯中,內(nèi)燃摻配比例高低不等,有摻配所需熱耗的60%,有摻配高達80%,少數(shù)磚廠采用全內(nèi)燃燒磚,內(nèi)燃摻配達到100%。
摻配比例較低的,則需要在隧道窯投煤孔外投少量原煤作為熱量補充,而摻配比例較高的磚坯,焙燒過程中,則基本不用外投煤即能夠完成制品燒結(jié)。因此,內(nèi)燃燒磚工藝中,產(chǎn)品具有燃料性質(zhì),“產(chǎn)品就是燃料、燃料就是產(chǎn)品”,成為現(xiàn)有燒結(jié)磚工藝中的主要特征之一。
產(chǎn)品中含有可燃物的內(nèi)燃摻配方式,使得制品在焙燒過程中,因局部處于還原氣氛的影響,制品表面會出現(xiàn)“壓花”、內(nèi)部會出現(xiàn)“黑心”等缺陷,這些成了內(nèi)燃磚的一種符號。
B、強氧化燃燒特性
內(nèi)燃燒磚工藝將燃料和原料混為一體,燃料在磚坯中均勻分散,“你中有我,我中有你”擠出成型后,磚坯成為一種發(fā)熱值較低的特殊“燃料”。
內(nèi)燃燒磚的燃燒過程中,由于“燃料”形態(tài)的改變,焙燒時窯內(nèi)氧化高溫,逐步由坯體表面向坯體內(nèi)部擴散,鑒于坯體較密實,氧氣滲入坯體內(nèi)部困難,為了克服這種不利現(xiàn)象,應(yīng)采取如下兩個方面措施:
選擇合理的碼垛形式
在隧道窯內(nèi)燃燒磚工藝中,燒窯師傅常常提到“七分碼、三分燒”的口頭禪,意思就是隧道窯燒磚的產(chǎn)品質(zhì)量好壞、產(chǎn)量高低、能耗多少,與坯垛的形式有著密切聯(lián)系。燒窯師傅經(jīng)驗證明,內(nèi)燃燒磚應(yīng)遵循“邊密中稀、上密下稀”的原則,在此原則基礎(chǔ)上進行適應(yīng)性調(diào)整以保證截面溫度的均勻,實現(xiàn)高產(chǎn)和低耗的目標。
努力降低系統(tǒng)阻力
燃料的燃燒,離不開助燃空氣,內(nèi)燃燒磚所需的助燃空氣,全部由隧道窯出車端進入,冷空氣通過冷卻帶、高溫帶和預(yù)熱帶,經(jīng)風機送入干燥室成為干燥介質(zhì),全窯系統(tǒng)阻力,對于煙氣的流動影響較大,即使采用較好的碼坯方式,磚垛截面溫度不均勻的現(xiàn)象仍然難免,為此,除相鄰坯體之間留有一定間隙,相鄰坯垛之間需要留有合適的火道,以便高溫由坯體表面?zhèn)鬟f到坯體內(nèi)部。就煙氣的流動而言,還需要克服由窯體、窯車、哈風閘、坯垛、窯門等構(gòu)成的系統(tǒng)阻力,當按照規(guī)定的焙燒制度進行焙燒時,則需要高溫煙氣具備較強的動壓。這也是隧道窯焙燒特性及“內(nèi)燃焙燒”性質(zhì)所決定的。強調(diào)降低系統(tǒng)阻力,成為內(nèi)燃+外投煤焙燒方式中,強氧化燃燒的特征之一。
C、溫度區(qū)間的移動
現(xiàn)有的隧道窯內(nèi)燃燒磚熱工系統(tǒng)中,設(shè)置了余熱利用功能,普遍的做法,是窯內(nèi)高溫煙氣經(jīng)哈風口、支煙道、總煙道由風機抽取,作為干燥介質(zhì)送入干燥室干燥濕坯體,經(jīng)干燥后的坯體干坯再進入隧道焙燒窯,能夠節(jié)約干燥過程的熱量消耗。必須強調(diào)的是,風機抽取窯內(nèi)煙氣時,首先要保證窯內(nèi)正常焙燒,其次才是滿足煙氣的余熱利用。應(yīng)該避免的是,當出現(xiàn)內(nèi)燃摻配波動、外投煤過量、進車不及時、意外停電等狀況時,窯內(nèi)溫度區(qū)間將因風機的持續(xù)抽力作用而產(chǎn)生移動,造成焙燒質(zhì)量下降,廢品率提高,能耗上升。
D、溫度控制的滯后
隧道窯內(nèi)燃+外投煤焙燒方式,燃燒過程與助燃空氣的風量相關(guān),隨著氧量愈充足,燃料燃燒愈快,窯內(nèi)火行速度也較快。然而,由于入窯坯體還有6%左右的殘余水分,此時如對窯內(nèi)溫度不加控制,坯體殘余水分脫除速度太快,坯體極易出現(xiàn)裂紋。對焙燒溫度控制的措施,一般通過調(diào)整哈風閘、風機風量、進車時間等手段,這些措施的使用,只能由崗位工通過提前預(yù)判進行,一旦超高溫度已經(jīng)形成,這些控制辦法并不能馬上奏效,調(diào)控效果滯后,使得即使同一個窯車上的產(chǎn)品,形成磚垛內(nèi)部過燒變形,而磚垛邊部欠火,形成“內(nèi)燃燒磚”焙燒過程中必須倚重看火工的現(xiàn)象,人為因素對燒成質(zhì)量的影響太重。
E、工藝控制較寬泛
隧道窯內(nèi)燃+外投煤焙燒方式,具有工藝控制較寬泛的特征,主要表現(xiàn)為以下三點。
首先,入窯干坯殘余水分發(fā)生波動,水分為6~8%的波動范圍時,焙燒過程中不會出現(xiàn)控制困難,崗位工對隧道窯工況的調(diào)整比較容易。其次,生產(chǎn)負荷具有一定彈性,意味進車時間比較靈活,提高產(chǎn)量的能力較強,這是“內(nèi)燃燒磚”的優(yōu)勢之一。第三,即使實際燒成曲線與預(yù)定燒成曲線的偏差較大,也不會嚴重影響焙燒質(zhì)量。
上述5點關(guān)于隧道窯內(nèi)燃+外投煤焙燒方式的特征描述,在燒結(jié)磚生產(chǎn)中具有一定代表性。
2、液化天然氣(LNG)與氣化氣的技術(shù)參數(shù)
天然氣是一種清潔燃料,目前國內(nèi)一般工業(yè)企業(yè)天然氣的應(yīng)用方式,一種方式為液化天然氣(LNG)+氣化站+氣化氣應(yīng)用,其次,直接取用管道天然氣。
燒結(jié)磚企業(yè)采用管道天然氣時,能夠省卻液化天然氣(LNG)氣化站的建設(shè)及管理,對管理和技術(shù)能力較為薄弱的企業(yè),就生產(chǎn)和安全兩方面而言,較為省心,是燒結(jié)磚隧道窯“煤改氣”技術(shù)方案的首-選。
如果輸送天然氣管道敷設(shè)不到位,無法使用管輸天然氣供氣時,企業(yè)隧道窯“煤改氣”的氣源保障方案,只能采用建設(shè)液化天然氣(LNG)氣化站“低溫存儲、常溫使用”的方式,氣化站建設(shè)周期短,能迅速滿足企業(yè)用氣要求,成為企業(yè)固定供氣設(shè)施或管輸天然氣到達前的過渡供氣設(shè)施。
圖1、2為貴州省某燒結(jié)磚企業(yè)與燃氣公司共同建設(shè)的自備液化天然氣氣化站,液化天然氣(LNG)采用專用槽車運輸。
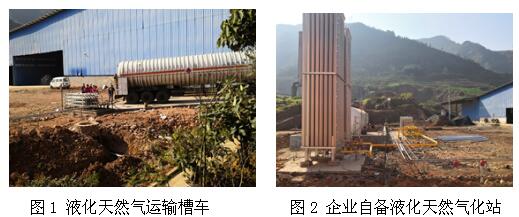
資料介紹,標準狀態(tài)下,液化天然氣(LNG)和天然氣的技術(shù)參數(shù)如下。
LNG單位換算:
LNG密度(430Kg/m³)是標準狀態(tài)下甲烷的625倍,即1m³LNG可氣化成625m³天然氣。
(1m³LNG=0.45噸LNG,即1噸LNG=2.2m³LNG),故1噸LNG可氣化為1375m³天然氣。
LNG儲罐:
50m³儲罐=50m³*0.45噸=22.5噸 ,
可存儲:22.5噸*1375m³=30938m³天然氣。
1㎏ LNG≈1.4-1.5m³ 天然氣;
1㎏ LNG≈1.33L 柴油;
1㎏ LNG≈1.63L 汽油;
1m³ LNG可氣化600-625m³ 天然氣;
1m³ LNG的質(zhì)量≈430-470㎏。
1L LNG=0.001m³ LNG≈0.6-0.625m³ 天然氣;
1L LNG=0.001m³ LNG,其質(zhì)量≈0.43-0.47㎏
1m³ 天然氣≈0.7256㎏ LNG
1m³ 天然氣 折0.65-0.75公斤
據(jù)估算,滿足年產(chǎn)8000萬塊(折標磚)燒結(jié)頁巖空心磚生產(chǎn)線“煤改氣”所需氣源用量的液化天然氣氣化站,設(shè)備及安裝投資(不含土建費用)約120~140萬元。
3、隧道焙燒窯“煤改氣”的實踐
2017年5月,貴州省某燒結(jié)磚廠,采用內(nèi)燃摻配料+外投煤(內(nèi)
燃燒磚)工藝方式進行燒結(jié)磚生產(chǎn),主要原料為頁巖,內(nèi)燃摻配料品種為鍋爐渣、泥煤、煤矸石等,由于該地區(qū)原煤含硫量較高,使得鍋爐渣、泥煤、煤矸石等摻配料的二氧化硫含量相應(yīng)偏高,生產(chǎn)中,即便對大氣污染物治理采用全生產(chǎn)過程管理模式,但達標排放不能持續(xù)穩(wěn)定,生產(chǎn)不能穩(wěn)定進行。企業(yè)*終確定改變?nèi)剂辖Y(jié)構(gòu),經(jīng)過與燃氣公司協(xié)調(diào),決定采用天然氣替代“內(nèi)燃摻配料+外投煤”,并對隧道焙燒窯的外投煤系統(tǒng)進行“煤改氣”的技術(shù)改造,隧道窯改用氣燒。
3.1磚廠概況
該長,年生產(chǎn)規(guī)模為8000~10000萬塊(折標磚)燒結(jié)頁巖空心磚,生產(chǎn)線工藝流程及技術(shù)參數(shù)如下。
該生產(chǎn)線采用“一次碼燒內(nèi)燃燒磚”工藝,生產(chǎn)配比為頁巖:泥煤:煤渣=76:5:19,磚坯發(fā)熱值達到280∽320kCal/kg,摻配比例能夠保證成品的單位產(chǎn)品能源消耗滿足標準限額要求。
該長的生產(chǎn)線中有內(nèi)寬4.8米、長度90米隧道干燥窯2條,內(nèi)寬4.8米、長度132.6米吊平頂隧道焙燒窯2條(雙通道窯)。隧道焙燒窯為內(nèi)置煙道,進車端設(shè)置哈風口9對、出車端設(shè)置哈風口8對,預(yù)熱帶第11車位至高溫帶末端第23車位,共設(shè)置36排投煤孔計144個,排間距為1250mm,投煤孔區(qū)間距離約為43米,12個車位。全窯窯車容車量為34輛。
隧道焙燒窯煙氣由2臺18號離心風機將全部煙氣送人干燥隧道窯,熱交換后,再經(jīng)2臺20號離心風機抽至總道匯合后送人50米煙囪底部脫硫系統(tǒng),除塵脫硫和除霧后經(jīng)煙囪出口排放。
脫硫采用鈉鈣“雙堿法”
3.2隧道焙燒窯“煤改氣”內(nèi)容
內(nèi)容有:液化天然氣(LNG)氣化站和隧道窯燃氣系統(tǒng)建設(shè)兩部分。
液化天然氣(LNG)氣化站的建設(shè),依靠燃氣公司委托有資質(zhì)單位承擔氣化站設(shè)計,設(shè)計規(guī)范為:GB 50028—2006《城鎮(zhèn)燃氣設(shè)計規(guī)范》、GB50016-2006《建筑設(shè)計防火規(guī)范》、GB 50183—2004《石油天然氣工程設(shè)計防火規(guī)范》,氣化站見圖1、圖2,一般流程如下。
槽車將液化天然氣(LNG)送至氣化站內(nèi)低溫儲罐內(nèi)儲存,當由儲罐外排時,先通過儲罐的自增壓系統(tǒng),使儲罐壓力升高,然后打開儲罐液相出口閥,通過壓力差將儲罐內(nèi)的(LNG)送至空溫式氣化器,氣化器出口的天然氣溫度如低于5℃時,需在出口串聯(lián)水浴式加熱器,對氣化后的天然氣進行加熱。再經(jīng)調(diào)壓、計量、加臭等工序后送入窯爐用氣管網(wǎng)。
隧道窯外燃天然氣燃燒系統(tǒng)建設(shè),主要由窯爐公司承擔。
本次隧道焙燒窯燃氣系統(tǒng)改造,根據(jù)焙燒曲線、現(xiàn)有4.8米×3.9米窯車規(guī)格、碼坯方式為4垛×3排時,系統(tǒng)改造中取消原投煤孔布置形式,窯面天然氣燒嘴改為每排5個,磚垛排橫向間距則分別為300mm,燒嘴每排間距為1300mm。燒嘴數(shù)量共計180個,區(qū)間長度為45米,窯車車位11.5輛,由進車端第8車位開始布置,截止在高溫帶末端的第20車位。隧道焙燒窯為雙通道聯(lián)體窯,兩側(cè)墻未考慮設(shè)置燒嘴。
燒嘴口增加碳化硅保護,預(yù)防高溫返火對燒嘴的損害。
每個燒嘴配置助燃空氣管道閥,與天然氣進行配合,以便調(diào)整火焰溫度和燃燒強度。
燃燒系統(tǒng)設(shè)置熱電偶、燃氣調(diào)節(jié)閥、助燃空氣高壓風機變頻調(diào)速自動控制系統(tǒng),根據(jù)不同區(qū)域溫度要求,將燒嘴布置分為18個區(qū)域,通過設(shè)置熱電偶監(jiān)測窯內(nèi)溫度,同步調(diào)整18個區(qū)域內(nèi)天然氣自動調(diào)節(jié)閥,控制燃燒系統(tǒng),確保各區(qū)域窯內(nèi)溫度,與既定的溫度曲線一致。
隧道焙燒窯冷卻帶未進行改造,沿用原熱工控制裝置。換熱后余熱煙氣經(jīng)哈風閘、支煙道匯入總煙道由18號離心風機,送往干燥窯。
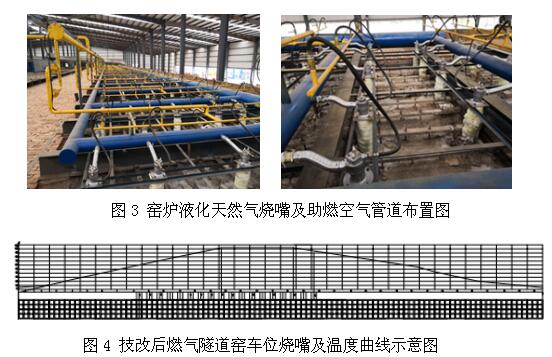
3.3隧道焙燒窯“煤改氣”后的生產(chǎn)
2017年7月,該燒結(jié)磚廠完成隧道焙燒窯“煤改氣”工作,經(jīng)燃氣氣化站和燃燒系統(tǒng)的調(diào)試,開始隧道窯點火,由于生產(chǎn)線停產(chǎn)時遺留的干坯及陳化庫內(nèi)原料還保留內(nèi)燃燒磚時的內(nèi)燃摻配比例,每塊磚坯發(fā)熱值達到280~320kcal/kg,滿足能耗限額標準要求。
采用常規(guī)的大灶車,點火過程中,兼顧隧道窯的烘窯程序,烘窯后,進車焙燒,產(chǎn)品見圖5。
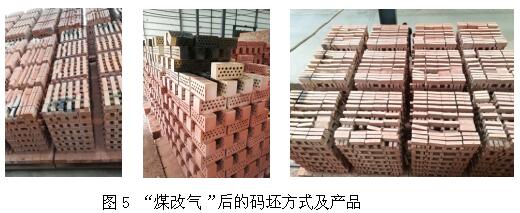
圖5顯示,4.8米×3.9米窯車的碼坯方式,依然采用原內(nèi)燃焙燒時的4垛×3排形式,垛、排之間保留縱向和橫向的煙氣通道,進車后,存在邊火眼火焰直接沖燒坯垛頂坯的現(xiàn)象,造成制品過燒。
由于坯體內(nèi)仍然具有熱值,因而,目前的生產(chǎn)過程控制及產(chǎn)品,還不能反映隧道窯用天然氣外燃焙燒的真實情況,不過,該廠的“煤改氣”的實踐,可以為其他燒結(jié)磚廠“煤改氣”的工作積累經(jīng)驗。
4、“煤改氣”的相關(guān)工藝條件分析
傳統(tǒng)隧道窯內(nèi)燃焙燒及煙氣余熱干燥系統(tǒng),是建立在內(nèi)燃摻配料+外投煤(內(nèi)燃燒磚)基礎(chǔ)上。 “煤改氣”后“內(nèi)燃燒轉(zhuǎn)”變“外燃燒磚”,固體燃料變氣體燃料。為了適應(yīng)這一變化,在窯爐結(jié)構(gòu)、碼坯形式等方面應(yīng)作出必要的改變和調(diào)整。
A、生產(chǎn)空心砌塊
眾所周知產(chǎn)品密度等級不同,生產(chǎn)能耗不同。如天然氣熱值為9000千卡/m3,生產(chǎn)不同密度產(chǎn)品,隧道窯焙燒消耗的燃氣量計算如下。
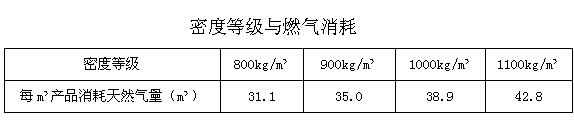
此時,每立方米800kg密度等級的產(chǎn)品,天然氣消耗量約31.1m3。而每立方米1100kg密度等級的產(chǎn)品,天然氣消耗量約42.8m3。每立方米密度相差300kg,燃氣消耗相差11.7m³。
參考貴州省2017年9月天然氣市場價調(diào)整,屬于省級定價區(qū)域的貴陽市城區(qū)及與其共用同一配氣管網(wǎng)區(qū)域的非居民用氣*高銷售價格從2.98元/立方米降為2.86元/立方米。
如果天然氣價格按照2.86元/立方米計算,800kg和1100kg兩種密度等級的每立方米產(chǎn)品天然氣費用,分別是88.95元和122.41元,兩者費用相差33.46元。
年產(chǎn)22萬m³燒結(jié)空心砌塊生產(chǎn)線,僅制品焙燒天然氣費用將達到1956.9萬元或2693.02萬元,因密度等級不同,兩者相差736.12萬元,燃氣費用增加部分,對于產(chǎn)品的市場競爭影響巨大。
隧道窯焙燒的“煤改氣”工藝方式,如果繼續(xù)生產(chǎn)墻體材料,必須實現(xiàn)產(chǎn)品完全空心化、低密度和大規(guī)格,從而降低燃氣費用,降低生產(chǎn)成本,提高產(chǎn)品價格和市場競爭力。否則,如果仍然選擇生產(chǎn)普通空心磚,則高昂的燃氣費用將難以維繼。具有裝飾功能的燒結(jié)磚,由于市場價格比普通磚高很多,隧道窯焙燒“煤改氣”后,燃氣費用增加部分,可以通過產(chǎn)品利潤提高、脫硫系統(tǒng)費用降低、工藝自動化程度提高、崗位工人員減少等成本降低而得到補償,因此隧道窯“煤改氣”焙燒裝飾功能的墻體材料,是可行的。但是,需要著重考慮裝飾制品的顏色、強度、不變形、不泛霜等裝飾功能要求。不僅對燃氣窯爐進行改造,同時需要對原料的配料及工藝控制參數(shù)進行完善。
B、低成型水分
在生產(chǎn)工藝中,濕坯干燥是必不可少的環(huán)節(jié),對于入窯干坯殘余水分而言,越低越好,以提高產(chǎn)品一級品率。針對生產(chǎn)具有裝飾功能的燒結(jié)材料而言,當殘余水分降低到1%,產(chǎn)品就不會出現(xiàn)壓印,減少泛霜缺陷。數(shù)據(jù)顯示,如采用傳統(tǒng)隧道窯焙燒普通磚,坯體入窯水分降低1%,焙燒每萬塊磚標煤耗量降低20~30kg,相當于節(jié)約天然氣15.5~23.3立方米。
采用低成型水分,才能為后續(xù)干燥環(huán)節(jié)降低殘余水分創(chuàng)造條件。低成型水分,不但與入窯殘余水分相關(guān),更重要的是,能夠降低干燥環(huán)節(jié)介質(zhì)消耗的能量,“煤改氣”后,干燥環(huán)節(jié)干燥介質(zhì)的用量、溫度與天然氣消耗密切相關(guān),當成型水分提高,干燥介質(zhì)用量增加,天然氣消耗和費用相應(yīng)提高。
C、設(shè)置無縱向煙道的碼坯方式
傳統(tǒng)內(nèi)燃燒磚隧道窯的助燃空氣由出車端進入窯內(nèi),由于在窯內(nèi)運行線路較長,同時,考慮窯內(nèi)磚垛截面溫度的均勻性,碼坯方式采用“邊密中稀、上密下稀”,的原則,窯車上坯垛與坯垛之間留有間距,根據(jù)窯車長度、坯垛規(guī)格、產(chǎn)品規(guī)格、投煤孔分布等技術(shù)參數(shù),間距尺寸變化較大。如國內(nèi)部分內(nèi)燃燒磚隧道窯,窯車長度為3.9米,3.75米,3.6米,磚垛規(guī)格如為1米*1米,坯垛排橫向間距則分別為300mm,250mm,200mm,生產(chǎn)實踐中,以利于內(nèi)燃焙燒產(chǎn)量的提高。
然而,這部分隧道窯“煤改氣”時,則需要考慮燃氣條件要求,如燃燒空間偏小,對磚坯焙燒均勻性和質(zhì)量存在不利影響。
國外燃氣隧道窯窯車規(guī)格中,長度為4.35米,坯垛規(guī)格為1米×1米,坯垛橫向間距為450mm,燒嘴間距為1450mm,能夠滿足燒嘴燃燒火焰所需空間要求。
窯車上坯垛縱向煙道,在內(nèi)燃隧道焙燒窯中,能夠降低通風阻力,有利提高產(chǎn)量,利于燃料的充分燃燒,然而 “煤改氣”后,助燃空氣直接配送到燒嘴,不再需要由出車端輸送空氣,經(jīng)坯垛縱向煙道的通風作用降低,此時,減少縱向煙道間距不會影響燃氣焙燒質(zhì)量和產(chǎn)量。
D、設(shè)置獨立的干燥熱介質(zhì)供應(yīng)系統(tǒng)
在傳統(tǒng)生產(chǎn)工藝中,干燥環(huán)節(jié)的干燥介質(zhì),來自焙燒窯內(nèi)余(煙)熱氣,通過風機抽取和輸送實現(xiàn)。當隧道窯改用天然氣后,干燥與焙燒仍然采用風機抽取和輸送聯(lián)系為一個系統(tǒng),容易出現(xiàn)焙燒控制難度增加的現(xiàn)象,影響焙燒質(zhì)量及燃氣的消耗,因此,隧道窯“煤改氣”技術(shù)方案中,應(yīng)通過準確的熱平衡計算,燒嘴風量計算,煙氣量計算,窯內(nèi)壓力控制,確定引風機的運行和窯內(nèi)哈風閘應(yīng)用的控制。
為了降低隧道窯燃氣控制的難度,有必要設(shè)置獨立、可控制的干燥熱介質(zhì)供應(yīng)系統(tǒng),能夠形成干燥與焙燒各自獨立運行或可控制的串聯(lián)運行,從而避免焙燒和干燥之間的互相影響和干擾。有利于燃氣窯的順利運行。
另外,設(shè)置獨立、可控制的干燥熱介質(zhì)供應(yīng)系統(tǒng),有利于嚴格控制磚坯殘余水分,滿足具有裝飾產(chǎn)品的焙燒要求。
E、提高窯體、窯車的保溫及密封等級
在隧道窯焙燒過程中,窯體越保溫,越密封,則越節(jié)約天然氣。因此,需要加強隧道窯窯頂和直墻保溫、煙道和哈風閘密封,對窯車,應(yīng)采用輕質(zhì)耐火材料砌筑,減少窯車砌筑材料儲熱損失,降低燃氣消耗。
窯車接頭,窯車與隧道窯砂封部位漏風,窯內(nèi)溫度波動,磚坯欠火,燃氣消耗增加。
傳統(tǒng)窯車襯砌常用重質(zhì)耐火材料、紅磚,吸熱及儲熱系數(shù)較大,不利燃氣隧道窯節(jié)能。窯車吸熱,對溫度影響較大,易造成磚垛下部溫度低,出現(xiàn)欠火。特別在傳統(tǒng)隧道窯改造中,由于不能設(shè)置兩側(cè)墻燒嘴,完全依靠窯頂燒嘴,如果燒嘴火焰長度不能調(diào)節(jié),磚垛下部溫度均勻性差,因此,窯車采用輕質(zhì)保溫墊層,對促使磚垛下部溫度均勻非常關(guān)鍵,在“煤改氣”進行中,窯車墊層的改造應(yīng)同時進行,這是隧道窯技改后能夠持續(xù)順利運行的重要條件。
F、可靠的燃燒系統(tǒng)自動控制
天然氣隧道焙燒窯的燒嘴布置,對窯橫截面溫度的均勻性有重要影響,隧道窯煤改氣方案,需要依據(jù)溫度曲線,設(shè)置燒嘴,也要依據(jù)窯內(nèi)溫度變化,設(shè)置各區(qū)間溫度監(jiān)測和天然氣、助燃空氣的自動化控制。對于寬斷面隧道窯,由于橫截面寬,布置的燒嘴數(shù)量多,如果對燒嘴燃燒后該區(qū)間溫度變化沒有及時調(diào)整,會出現(xiàn)溫度持續(xù)升高或焙燒溫度不能滿足燒結(jié)的缺陷。
其次,一排燒嘴之間,同樣存在上述不利的焙燒情況,因此對隧道窯煤改氣的技術(shù)方案,需要根據(jù)溫度曲線,進行溫度監(jiān)測及燒嘴燃燒中天然氣和助燃空氣的自動化控制,燒嘴燃燒控制,必須確定為所有燒嘴都能單獨控制和調(diào)整,在寬斷面隧道窯的燃氣自動化控制中,實現(xiàn)所有燒嘴燃燒強度的單獨自動控制,這是精確控制全窯溫度曲線的基本條件,是節(jié)約天然氣的基本條件,同時,也是獲得高產(chǎn),高品質(zhì)產(chǎn)品的基本條件。
需要注意的是,傳統(tǒng)隧道窯窯車上碼坯高度存在差異,各廠不同,碼高12、13、14層不等,甚至存在碼高16層的,此時,“煤改氣”的技術(shù)方案,除需要配置適宜的天然氣壓力和助燃空氣高壓風機外,還必須考慮燃氣燒嘴火焰長度能夠調(diào)節(jié),否則,磚垛截面溫度的均勻性將降低,產(chǎn)品質(zhì)量差異和產(chǎn)品外觀色差較大。
G、建立自動卸磚打包
應(yīng)該說,需要進行煤改氣的隧道窯焙燒磚廠,在生產(chǎn)線中,往往缺乏自動化的卸磚環(huán)節(jié) ,部分企業(yè)雖然設(shè)置有半機械的卸磚環(huán)節(jié),如人力卸磚機械打包叉車堆碼及裝車的過程,窯車車面上,存在工人卸磚時產(chǎn)生的活動荷載,對窯車保溫墊層,車面平整度,窯車之間的曲封嚴密性等帶來負面影響致使窯焙燒時出現(xiàn)漏氣,溫度波動,欠火,燃料消耗增加。對此,煤改氣的方案中,必須將窯車成品自動化卸磚的設(shè)備及方式,作為重要內(nèi)容并及時實施。從而確保煤改氣后,燃氣消耗低,產(chǎn)品質(zhì)量好。如果企業(yè)因資金所限暫時不能實施自動化卸磚,那么,企業(yè)應(yīng)采取補救措施,建立人工對窯車保溫、墊層、曲封等部位的及時修復(fù)制度。
H、保留大氣污染物治理及監(jiān)測系統(tǒng)
“煤改氣”后避免大氣污染物中顆粒物超標排放成為重點。
隧道窯的燃料煤改氣后,企業(yè)原有的大氣污染物治理系統(tǒng),應(yīng)繼續(xù)保留并照常運行。天然氣的燃燒過程中,煙氣中二氧化硫成分較低,通過燃料結(jié)構(gòu)改變,從根本上避免煙氣中產(chǎn)生二氧化硫,使得原有治理系統(tǒng)中針對脫硫需要添加的脫硫劑如氫氧化鈉、石灰,添加量將大幅度降低,污染物SO2可達標排放。但是,需要考慮排放標準中關(guān)于顆粒物排放量指標,其30mg/立方米的控制指標同樣很嚴格,煙氣要滿足達標排放,不會是燃料結(jié)構(gòu)改變一個條件就能實現(xiàn)的。天然氣燃燒過程,需要助燃空氣量達到1比10左右。窯車,煙道,磚坯表面因大量氣流沖刷,閘閥變動等因素引起的顆粒物數(shù)量,隨著產(chǎn)量的提高,而有所增加,決不會因采用燃燒天然氣而無顆粒物排放。
因此,磚廠原有治理系統(tǒng)應(yīng)針對顆粒物的達標,保持正常的運行和管理。
5、結(jié)束語
當前,我國正實施全面建成小康社會戰(zhàn)略和鄉(xiāng)村振興戰(zhàn)略,鄉(xiāng)鎮(zhèn)建設(shè)廣泛普及,建筑形式多樣,為了與當?shù)丨h(huán)境特點、功能要求和諧一致,對建筑物外觀色彩,建筑周邊道路材料材質(zhì)和顏色,要求眾多,不僅提出適合中國建筑特色的樣式和色彩元素,還有很多建筑,具有低層、個性化、與環(huán)境和諧、色彩豐富的歐洲建筑形式。而這些建筑和色彩要求,*好的建筑材料,就是采用“煤改氣”后燒成燒結(jié)空心磚、空心砌塊、清水墻磚、道路磚等。這部分產(chǎn)品市場需求,恰恰是傳統(tǒng)內(nèi)燃隧道焙燒窯必須進行“煤改氣”的動力,通過對隧道窯“煤改氣”工藝條件分析,建議如下。
A、應(yīng)立足采用管道氣源為主,避免建設(shè)天然氣氣化站所需要的建設(shè)條件、燃氣系統(tǒng)操作安全規(guī)范等必須條件。如考慮建設(shè)天然氣氣化站,其設(shè)計及建設(shè)必須滿足國家標準要求,安全可靠。
B、節(jié)約天然氣消耗是煤改氣后必須高度關(guān)注的核心問題,應(yīng)該從煤改氣技術(shù)方案,窯爐、窯車系統(tǒng)保溫密封,產(chǎn)品結(jié)構(gòu)組成,自動化控制等方面進行周密詳盡的安排,對于舊窯的煤改氣方案中,窯頂燒嘴布置和數(shù)量,兩側(cè)墻燒嘴布置和數(shù)量,自動化控制要求,應(yīng)根據(jù)窯車規(guī)格,碼坯形式,進行安排,不能僅僅將燒嘴布置在原窯頂投煤孔內(nèi)就認為實現(xiàn)了“煤改氣”。
C、建立獨立的干燥介質(zhì)供應(yīng)系統(tǒng),采用隧道窯冷卻帶空氣與
產(chǎn)品換熱的余熱空氣作為干燥介質(zhì),獨立提供的干燥介質(zhì)與換熱得到余熱干燥介質(zhì),可實現(xiàn)并聯(lián)運用或兩者串聯(lián)應(yīng)用,能夠形成干燥與焙燒各自獨立運行或可控制的串聯(lián)運行,提高燃氣綜合熱效率。換熱后的這部分余熱空氣,是沒有污染物的干凈煙氣,可不用治理。
D、隧道窯“煤改氣”后,可采用單一原料或不同原料種類搭配,突出燒結(jié)制品裝飾功能,提高產(chǎn)品附加值。
E、內(nèi)燃焙燒依靠窯內(nèi)通風量控制預(yù)熱帶,高溫帶的溫度制度,而
天然氣外燃焙燒則以燒嘴燃燒強度控制窯內(nèi)溫度制度,與窯內(nèi)通風量的關(guān)系相對降低,磚垛縱向煙道的作用減小。
F、依靠調(diào)整進車時間,或調(diào)整進車數(shù)量來穩(wěn)定隧道窯三帶的方式,在燃氣隧道焙燒窯的熱工控制中,并不是合理和經(jīng)濟的方式,燃氣隧道窯溫度曲線相對比較固定,通過燒嘴燃燒強度穩(wěn)定下來,不能通過窯車進車時間或進車數(shù)量來調(diào)整。
G、隧道窯“煤改氣”后,原煙氣治理系統(tǒng)中,脫硫劑氫氧化鈉、石灰,系統(tǒng)維護、防腐設(shè)施等方面的的消耗,能夠大幅度降低,能夠彌補采用天然氣費用的增加。
天然氣氣源的保證、產(chǎn)品大規(guī)格、高空洞率、低密度、低傳熱系數(shù)墻體材料和具有強度高、色差小、色彩豐富的裝飾功能的墻體材料的市場需求等條件,對“煤改氣”后降低生產(chǎn)成本、提高企業(yè)效益具有重要意義,如果“煤改氣”后的企業(yè),氣源得不到保障、產(chǎn)品仍然以燒結(jié)普通磚為主,那么,生產(chǎn)成本增加、效益低下,企業(yè)將會出現(xiàn)難以為繼的困擾。
參考文獻:
燒結(jié)磚瓦工藝 殷念祖,北京:中國建筑工業(yè)出版社, 1982.
燒結(jié)磚瓦廠工藝設(shè)計 西北建筑設(shè)計院,北京:中國建筑工業(yè)出版社, 1982.
天然氣隧道窯應(yīng)用與前景 周禮國《磚家》2017.12
來源:中國磚瓦工業(yè)燒結(jié)技術(shù)信息中心網(wǎng)